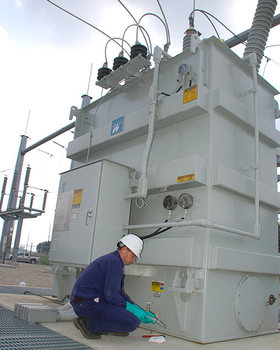
Large power transformers are some of the most reliable assets used in electrical power systems. Even so, they can and do fail. Transformer failures can cost you millions in lost production, income and customers. Through regular transformer testing and maintenance, you can uncover developing problems before they escalate. This enables proactive repair that supports system reliability and business continuity.
Vertiv brings some of the industry’s most skilled electrical testing, maintenance, and engineering experts to your plant to ensure your transformer can provide reliable power for your business. Through routine inspections, we collect information on transformer performance, analyze the records, and look for significant trends or signs of impending failure. With this information, you are able to make smarter decisions about your electrical assets, so you can improve every aspect of electrical system reliability and avoid unplanned outages.
More information Manufacturer's Website
Technical Summary
Substation Maintenance
On-site transformer and substation services can be individually performed by the NETA-certified technicians of Vertiv™ or combined as a complete package to improve reliability. The services include:
Transformer assembly, installation and removal
- On-site inspection and testing
- Insulation testing
- Fluid/oil analysis and condition trending
- Insulating fluid/oil reconditioning
- Failure/fault analysis
- Tap changer repair/replacement
- Leak repairs y Gasket/bushing repair
- Substation grounding
- Cooling upgrades
- Emergency services 24x7
Turnkey Installation
Vertiv provides complete turnkey installation, replacement, upgrades, removal, and disposal of your electrical equipment. Our technical staff will provide complete design, installation, commissioning, and maintenance services for most transformers and related equipment.
Commissioning and Startup
The successful operation of a transformer is dependent on proper design, installation and startup. Our services will verify that equipment has been properly installed to ensure reliable operation. Highly qualified personnel will use technologies and tests including the following:
Function Testing of Protection Controls
Testing is performed to ensure all protective devices are operating within normal specifications.
Insulation Power Factor Testing
Used to measure dielectric losses, insulation power factor testing determines the overall insulation condition of the windings, barriers, tap changers, bushings, and oil.
Transformer Turns Ratio Testing
This testing measures the turns ratio of the transformer on the primary and secondary coils. It also verifies the actual voltage matches the specified voltage ratio from the initial design.
Insulation Resistance Testing
By applying voltage to the dielectric barrier and measuring against specifications, this testing verifies insulation integrity and proper installation.
Winding Resistance Testing
This type of testing ensures correct connections and that there are no severe mismatches or open connections.
Frequency Response Analysis
Frequency response analysis compares input voltages to output voltages in order to determine whether there is any damage to the transformer windings that may have occured during shipment or installation.
Preventive Maintenance
The ongoing efficiency of electrical systems requires proper analysis, interpretation, and service recommendations. Experienced Vertiv field technicians provide complete preventive maintenance testing services to ensure the reliable operation of new and existing transformers. Using the same technologies and techniques previously described, our experienced technicians will compare results against baseline measurements to determine overall transformer health.
Online Predictive Maintenance
Our online predictive maintenance services can be performed while your system remains energized, eliminating costly shutdowns. By performing the following services, we can help you identify when a failure may occur so you can plan an outage instead of dealing with an emergency.
Visual Inspections
Using visual inspections as part of your predictive maintenance program allows you to check cleanliness, as well as cracked insulators and bushings, condition of paint, oil levels, oil leaks, oil/winding temperature gauges, nitrogen pressures, relay targets, and condition of grounds.
Infrared Testing
Identifying precursors to failure is possible with infrared testing that detects heat buildup, loose connections, and defective surge arrestors.
Ultrasonic Detection
This type of testing identifies excessive corona which produces radio-frequency interference and may cause an insulator, bushing, or surge arrester to fail.
Manuals
Technical Specs
Resources
Related Pages
- Arc Flash Studies and Training
- Circuit Breaker Testing
- Energy Recommendations - Return on Investment
- Electrical Assessment
- Electrical Safety Training
- Ground Fault Testing
- Harmonic Mitigating Transformers
- Infrared Services
- Load Testing
- Medium Voltage Transformers
- NERC Compliance Services
- One-Line Diagrams
- Partial Discharge Testing
- Permanently Mounted Sensors
- Power Quality Studies and Harmonic Analyses
- Power System Reliability Studies
- Protective Relay Maintenance and Testing
- Power System Reliability Studies
- Safety Audits
- Short Circuit and Coordination Studies
- Thermal Control Optimization
- Transformer PM
- Ultra-Efficient Transformers